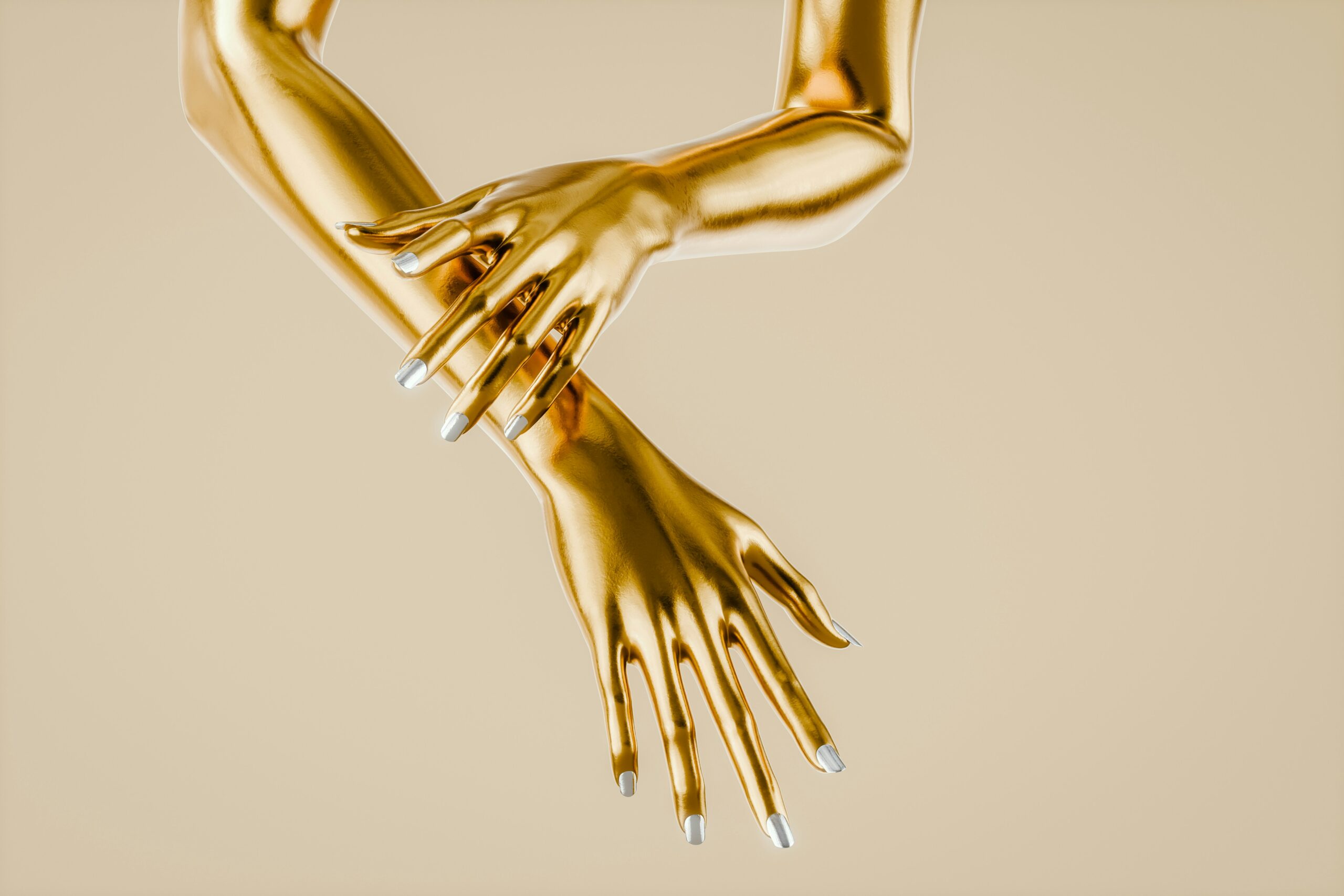
Integrating 3D printing into orthopedic implants has reshaped the industry, offering innovative solutions for patients and practitioners. Traditional manufacturing methods often face challenges in meeting individuals’ unique anatomical requirements. With 3D printing, these hurdles are overcome, resulting in implants tailored to each patient’s needs. This shift has enhanced surgical outcomes, improved patient comfort, and increased overall satisfaction.
Moreover, 3D printing has opened the door to new possibilities for material usage. Traditional implants relied heavily on metals like titanium or cobalt-chromium alloys. In contrast, 3D printing allows for a broader range of materials, including biocompatible polymers and composites. These materials mimic the properties of natural bone, making them an excellent choice for orthopedic applications.
Personalized Implants: A Leap Forward
One of the most significant advantages of 3D printing in orthopedics is the ability to create personalized implants. Every human body is unique, and injuries or conditions often require customized solutions. Traditional implants come in limited sizes and shapes, sometimes leading to complications during surgery or recovery.
With 3D printing, surgeons can design implants based on precise patient data, often obtained from CT or MRI scans. This customization ensures a perfect fit, reducing surgical time and improving healing. For example, in cases of complex joint replacements, 3D-printed implants align perfectly with the patient’s anatomy, offering superior functionality and comfort.
Additionally, 3D printing enables the production of implants with porous structures, mimicking natural bone. This feature encourages bone ingrowth, leading to better implant integration and reducing the risk of rejection or complications.
Cost-Effectiveness and Accessibility
Cost has always been a barrier in advanced medical procedures, including orthopedic surgeries. Traditional manufacturing processes involve multiple stages, expensive machinery, and considerable waste. 3D printing addresses these challenges by streamlining production.
With additive manufacturing, material wastage is minimal since the process involves building the implant layer by layer. This efficiency not only reduces costs but also minimizes the environmental impact. Additionally, 3D printing’s rapid prototyping capabilities allow for faster development of new designs, shortening the time required to bring innovations to market.
This cost-effectiveness can make high-quality orthopedic care accessible to a larger population. In regions with limited resources, 3D printing labs can produce affordable implants locally, eliminating the need for costly imports and reducing logistical delays.
Enhancing Surgical Training and Planning
The role of 3D printing extends beyond implant manufacturing; it also plays a crucial part in surgical planning and training. Surgeons can use 3D-printed models of a patient’s anatomy to plan complex procedures more precisely.
For example, a detailed 3D model provides invaluable insights into the best surgical approach in cases involving intricate deformities or fractures. These models allow surgeons to practice and refine their techniques before the actual procedure, reducing risks and improving outcomes.
In medical education, 3D-printed anatomical models are becoming indispensable tools. Unlike cadavers, these models can be tailored to showcase specific conditions or anomalies, offering students a more comprehensive learning experience. The tactile feedback and visual clarity provided by 3D-printed models enhance understanding and skill acquisition.
Future Trends and Innovations
The future of 3D printing in orthopedics holds immense promise. Researchers are exploring using bio-inks to print implants embedded with living cells, paving the way for regenerative solutions. Such advancements could eliminate the need for replacement surgeries by encouraging the natural regrowth of damaged tissues.
Another exciting development is the integration of innovative technologies into 3D-printed implants. Sensors embedded in the implants can monitor healing progress and detect potential issues, allowing timely intervention. These innovative implants could revolutionize post-operative care, reducing complications and enhancing recovery rates.
Furthermore, advancements in software and design tools are making creating 3D-printed implants even more efficient. AI-driven algorithms can optimize implant designs for strength, weight, and biocompatibility, ensuring superior performance.
Challenges and Ethical Considerations
Despite its numerous advantages, adopting 3D printing in orthopedic implants is challenging. Regulatory approvals for new materials and designs can be time-consuming, delaying availability in clinical settings. Ensuring the long-term safety and durability of 3D-printed implants is another critical concern.
Ethical considerations also come into play, particularly regarding the equitable distribution of this technology. While 3D printing has the potential to make implants more accessible, disparities in access to advanced healthcare facilities could limit its benefits for specific populations.
Collaboration among researchers, manufacturers, and healthcare providers is essential to address these challenges. Establishing clear guidelines and standards for 3D printing in medicine will help ensure its safe and effective use while promoting widespread adoption.
3D printing is undeniably transforming the field of orthopedic implants, offering unprecedented levels of customization, cost-efficiency, and innovation. From personalized implants to enhanced surgical planning, the technology is improving patient outcomes and redefining standards in orthopedic care.
Integrating innovative technologies and bioengineering solutions promises even more incredible advancements as the industry evolves. By addressing existing challenges and ethical considerations, 3D printing can unlock a new era of accessible and effective orthopedic treatments.
The future of orthopedics is being shaped layer by layer, and 3D printing stands at the forefront of this transformative journey.