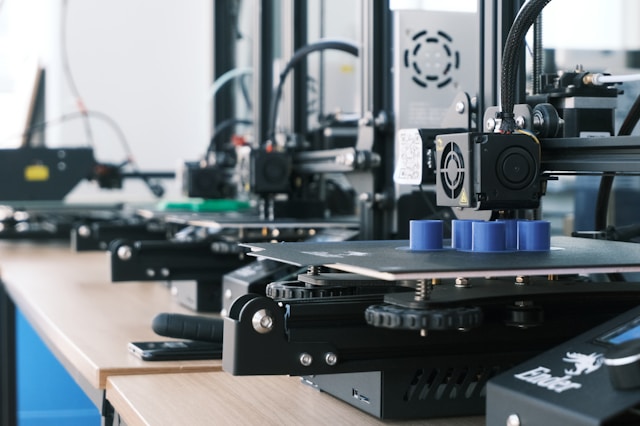
In recent years, 3D printing has emerged as one of the most promising technological advances in the medical field. It has opened up possibilities that were once thought impossible, particularly in creating customized medical devices. One area where 3D printing has a profound impact is the development of orthopedic implants. Traditional orthopedic implants have improved the quality of life for patients suffering from joint or bone injuries. However, these implants often follow a one-size-fits-all approach, which does not always guarantee a perfect fit for every patient. With the advent of 3D printing, orthopedic implants are being tailored to the exact specifications of the patient’s anatomy, which promises to improve outcomes significantly.
The Power of 3D Printing in Orthopedics
Orthopedic implants, which include devices like artificial joints and bone replacements, have been critical in modern medicine, helping people regain mobility and quality of life after accidents or degenerative conditions. Traditional implants are mass-produced in standard sizes, which may not suit every patient perfectly, leading to complications or less-than-optimal results. 3D printing, on the other hand, allows surgeons to design implants that match the unique shape and size of an individual patient’s bones and joints. This customizability enables a level of precision that traditional methods cannot achieve.
Moreover, 3D printing makes it possible to create complex internal structures in orthopedic implants that promote faster healing. For instance, lattice-like designs can improve bone growth around the implant, reducing the risk of implant loosening over time. These advancements could significantly enhance the effectiveness of implants, ensuring longer-lasting solutions for patients with joint problems or bone defects.
Benefits of 3D Printing for Implants
The ability to create personalized orthopedic implants using 3D printing offers several significant benefits, beginning with the customization of the implant itself. Unlike conventional implants, which are often mass-produced in a set of standardized sizes, 3D-printed implants are custom-designed to fit the patient’s specific anatomy. This approach reduces the chances of complications, such as improper fitting or discomfort, which can sometimes occur with traditional implants. A better fit leads to enhanced functionality and greater patient satisfaction, as it addresses each patient’s individual needs.
Another significant advantage of 3D printing is the speed at which implants can be produced. Traditional manufacturing processes for custom implants can be lengthy and expensive, often taking weeks or even months. With 3D printing, however, implants can be fabricated in a matter of days, allowing for quicker surgeries and reduced patient waiting times. In emergencies, this fast turnaround can make a life-changing difference, offering immediate solutions for patients needing urgent care.
In addition to faster production, 3D printing also offers cost advantages. While the initial cost of 3D printing equipment may be high, it can reduce long-term expenses. Since custom implants are designed with precision, there is less need for costly revisions or additional surgeries due to ill-fitting implants. Furthermore, 3D printing minimizes the likelihood of implant failure, which can reduce the need for follow-up surgeries that add to the financial burden.
Use of Advanced Materials
Additionally, 3D printing allows for using advanced materials like titanium, which is strong, lightweight, and biocompatible. These materials enhance the performance of the implants by making them more durable and able to withstand the pressures they will face within the human body. The customization and material properties work together to ensure that the implants perform better than their traditional counterparts, offering improved patient outcomes.
Finally, 3D-printed implants can also greatly enhance the patient’s comfort. A perfect fit reduces pain, improves mobility, and results in a faster recovery. With better-fitting implants, patients often experience fewer complications post-surgery and can return to regular activities more quickly. This improves the patient’s physical health and contributes to their overall emotional well-being, as they can regain their independence sooner.
Challenges and the Road Ahead for 3D Printing in Orthopedics
Despite the many advantages, the widespread adoption of 3D printing in orthopedic implants still faces some hurdles. One of the most significant challenges is the regulatory landscape. Medical devices, especially implants placed inside the human body, must adhere to strict safety and quality standards. 3D-printed implants are no exception, but obtaining regulatory approval for these products can be complicated. Regulatory agencies like the FDA must ensure that 3D-printed implants meet the required safety standards before being used in medical procedures. This process can be time-consuming and requires much scrutiny, which may slow the widespread use of 3D-printed implants.
Another challenge involves the materials used in 3D printing. While metals such as titanium are already used effectively for implants, researchers are continuously working to develop new, more advanced materials. These materials must meet rigorous standards for strength, durability, and biocompatibility to ensure they perform well over the long term. As material science advances, we can expect even more breakthroughs in the materials available for 3D printing in orthopedic applications.
3D Printing Equipment
Additionally, the cost of 3D printing equipment and the expertise required to use it can be prohibitive for some healthcare facilities, especially smaller hospitals or clinics. The technology requires specialized knowledge in design and production, and healthcare providers need to invest in training their staff to use these systems effectively. As the technology becomes more widespread, the costs are likely to decrease, but for now, the expense of 3D printing may limit its accessibility.
Training healthcare professionals is another critical element. Surgeons, orthopedic specialists, and other medical staff must have the skills to design and implement 3D-printed implants. This involves not only understanding how to use the equipment but also mastering how to assess and customize implants based on patient-specific data. As the use of 3D printing in orthopedics continues to grow, there will be a greater need for specialized training and ongoing skill development.
A Bright Future for Orthopedic Implants
Integrating 3D printing into the production of orthopedic implants is a groundbreaking advancement that is revolutionizing the field of orthopedics. By creating personalized implants that perfectly match a patient’s unique anatomy, 3D printing improves the precision, comfort, and performance of orthopedic surgeries. Although there are challenges related to regulation, material development, and cost, the future looks promising. With further research and technological development, 3D printing is set to become a cornerstone of modern orthopedic care, offering patients better outcomes and faster recovery times. The road ahead is exciting, and the potential benefits of 3D printing in orthopedics are vast, with innovations expected to continue shaping the future of medical treatments for years to come.