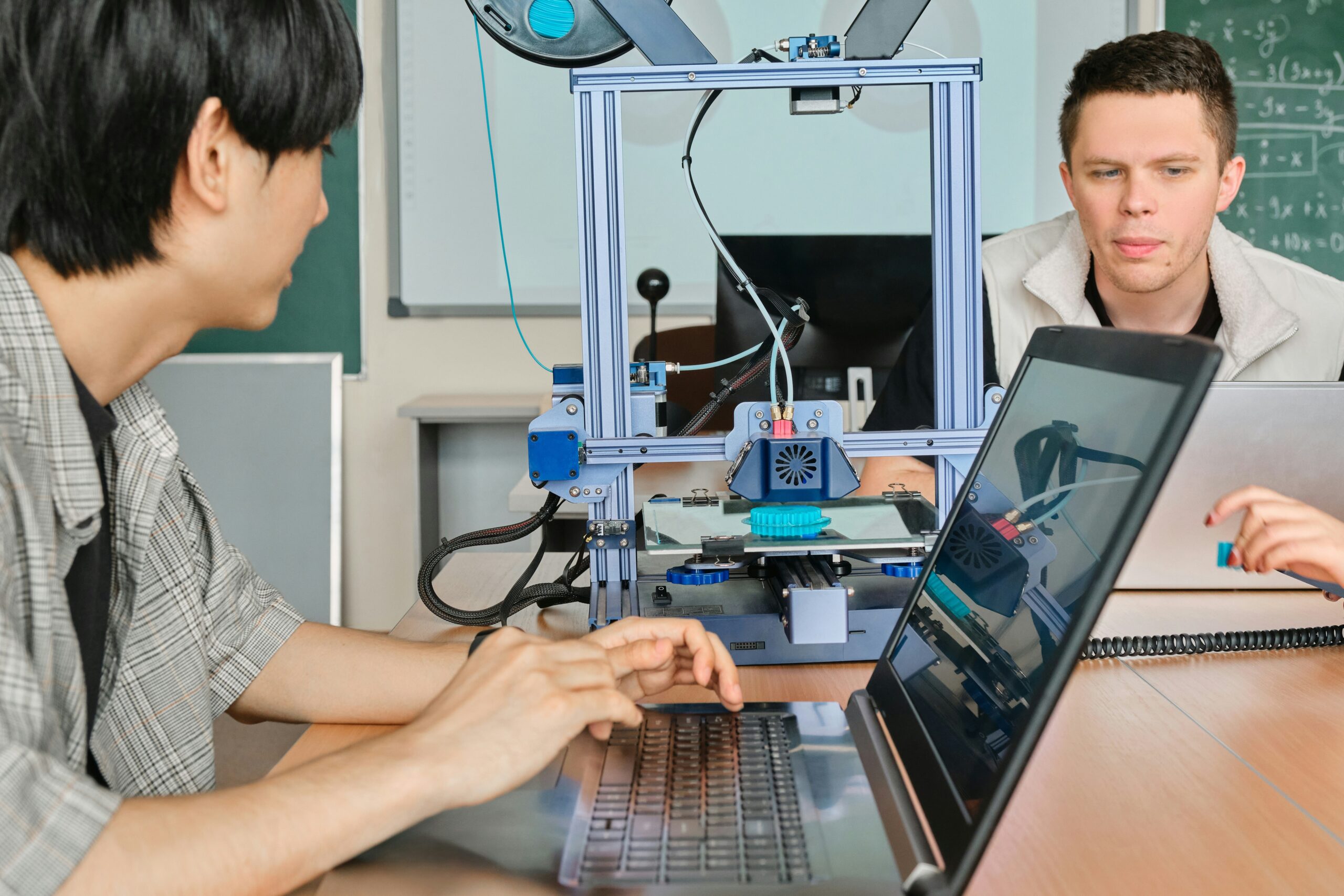
Orthopedic surgery has experienced numerous advancements in recent decades, but few innovations have generated as much excitement as 3D printing. This technology, also known as additive manufacturing, is transforming the design and production of orthopedic implants. By allowing for personalized, precise, and cost-effective solutions, 3D printing improves patient outcomes, reduces recovery times, and offers orthopedic surgeons new opportunities to provide tailored care. This article will explore how 3D printing is revolutionizing the orthopedic implant industry and what the future holds for this cutting-edge technology.
Understanding 3D Printing in Orthopedic Implants
3D printing in orthopedic implants involves creating customized implants by layering material based on digital 3D models. Unlike traditional manufacturing methods, which rely on molds or subtractive processes, 3D printing builds implants layer by layer, allowing for greater precision and flexibility. Surgeons can now design implants that perfectly fit the unique anatomical structure of individual patients, addressing the limitations of one-size-fits-all solutions.
One of the most significant advantages of 3D printing orthopedic implants is the ability to create custom implants for complex fractures, joint replacements, and deformities. This technology can also integrate materials like titanium, which is highly compatible with the human body and offers durability and strength.
The Benefits of 3D Printing for Orthopedic Implants
Personalized Solutions for Patients
Traditionally, orthopedic implants were mass-produced, and while they worked well for many patients, they often didn’t offer the best fit for those with unique anatomical challenges. 3D printing addresses this by creating custom implants tailored to the patient’s measurements. Surgeons can obtain a 3D scan of the patient’s bone structure, input the data into a computer, and design an implant that perfectly matches the patient’s needs.
This customization results in a more natural fit and can significantly reduce complications like implant loosening, misalignment, and excessive wear. Patients benefit from improved comfort, a better range of motion, and a faster recovery time, as the implant is designed to fit their body as if it were a natural part.
Enhanced Precision and Accuracy
One critical advantage of 3D printing is its precision. Traditional orthopedic implant methods rely on molds, which can introduce slight variations in the final product. With 3D printing, however, implants are produced with extraordinary accuracy down to microns, minimizing human error and ensuring a more precise fit.
This enhanced accuracy reduces the chances of surgical complications and helps improve long-term implant performance. Whether it’s a hip replacement or a knee prosthesis, the ability to tailor the implant precisely to the patient’s anatomy allows surgeons to achieve better outcomes.
Faster Production and Reduced Costs
In addition to improving precision, 3D printing streamlines the production process. Traditional methods of manufacturing orthopedic implants can be time-consuming, as molds must be created and tested before the final product is made. With 3D printing, however, surgeons and manufacturers can produce implants directly from a digital design, reducing production time significantly.
Faster production not only allows for quicker surgeries and more efficient resource use, but it can also lead to reduced costs. In the long term, healthcare providers may be able to lower the overall cost of implant surgeries by utilizing 3D-printed models. This also opens the door for better access to high-quality, personalized orthopedic implants for patients around the world.
Innovative Materials and Functionalities
3D printing in orthopedic implants isn’t limited to creating a custom shape; it also allows for using innovative materials that enhance the performance of the implants. For example, 3D-printed implants can incorporate bioactive materials or porous structures to encourage bone growth. This functionality, which is impossible to achieve with traditional manufacturing methods, can lead to more potent, durable implants that integrate better with the body.
Furthermore, the use of materials such as titanium, which is known for its biocompatibility and strength, ensures that these implants can withstand the body’s mechanical demands over time. As 3D printing technology advances, we may see even more materials introduced into the field, further enhancing the quality and lifespan of orthopedic implants.
3D Printing in Specific Orthopedic Applications
Joint Replacements
One of the most common applications of 3D printing in orthopedics is in joint replacement surgeries. Whether it’s hip replacements, knee replacements, or shoulder implants, 3D printing creates highly customized implants designed to fit the unique contours of the patient’s joint.
For example, in hip replacements, 3D printing can create a socket and ball joint that precisely matches the patient’s pelvic anatomy, improving the stability and longevity of the implant. This minimizes discomfort and optimizes the range of motion, making a significant difference in post-surgery recovery.
Spinal Implants
Spinal surgery often involves complex procedures, and 3D printing is proving to be an invaluable tool in spinal implant development. By using 3D printing, surgeons can produce implants perfectly shaped for the spine’s unique curvature, whether a vertebral cage or a spinal rod. These implants provide better stability and facilitate faster healing.
Additionally, the ability to 3D print spinal implants with a porous structure can promote the growth of bone tissue, allowing the implant to bond more effectively with the surrounding bone.
Bone Reconstruction and Fracture Repair
3D printing also plays a vital role in the repair of complex fractures or bone deformities. In cases where traditional bone grafting might not be sufficient, 3D-printed bone scaffolds can be used to fill in gaps or support the healing of bone tissue. These scaffolds can be designed to encourage bone regeneration, leading to a more effective and faster healing process.
In some cases, 3D printing has been used to print entire bones for reconstruction, particularly in patients with severe bone loss due to injury or disease. By creating implants that perfectly match the shape and function of the natural bone, 3D printing enables surgeons to restore standard bone structure and function with minimal invasiveness.
Challenges and the Future of 3D Printing in Orthopedics
Despite the many benefits, there are still challenges to overcome in the widespread adoption of 3D printing in orthopedic implants. Regulatory approval for new materials and implant designs can be lengthy, and the technology is still relatively expensive, making it less accessible in some healthcare settings.
However, as the technology matures and becomes more cost-effective, 3D printing will likely become a standard practice in orthopedic surgery. The potential for further innovations, such as 3D-printed implants capable of releasing medication or adapting to the body’s needs over time, could even further revolutionize the field.
3D printing is not just transforming how we think about orthopedic implants; it is fundamentally changing how they are made and used. 3D printing improves the quality of care for orthopedic patients worldwide by offering personalized solutions, improving precision, and reducing costs. As the technology continues to evolve, we can expect even more innovations to enhance patient outcomes and drive the future of orthopedic surgery.